5 Reasons to choose Ding Zhou to custom injection molding
Dingzhou Precision Injection Molding provides one-stop services, collaborates with you in all stages of product development, from rapid prototyping to production with our extensive knowledge and custom manufacturing, we support you in accelerating products to market .
Here, I will share two injection molding cases to demonstrate the professional capabilities, rich experience, and high quality service of the Ding Zhou team to you.
1.molded thread covers by plastic injection molding
Mould design
The mold adopts a three plate mold structure with one mold and two cavities. The external structure of the plastic part is molded by two sliding blocks colliding with each other, and the internal threads of the plastic part are molded by a threaded core,Due to the small demolding distance of the slider, it is driven by an inclined guide pillar. The inner hole of the plastic part is molded by a structure where the fixed model core collides with the moving model core.
Core structure
The structure of the plastic part determines that the internal thread must be demolded first, and then the two sliders are separated, with the gate set on the inner cylindrical surface of the plastic part to be molded. The core is divided into two layers: inner and outer,Install runners, gates, push rods, and pull rods on the inner core, and a structure for forming internal threads of plastic parts on the outer core.Due to the mold having a structure of 1 mold and 2 cavities, feeding is done from the ear protectors using a three plate mold frame. In order to install hydraulic cylinders, gear racksThe transmission mechanism composed of a driven gear thread core and a tapered roller bearing adopts a non-standard mold base. On the basis of the existing mold base,Add three plates between the moving template and the cushion block, namely gear fixing plate, core fixing plate, and cushion plate .
Injection molding flow marks solution:
The plastic shell of the energy storage power supply is injected into an injection mold with one mold cavity, and a three plate cold runner is used . After ABS injection molding, flow marks were found on the appearance surface.
Analyze the cause of the problem:
After discovering injection defects on the surface of the product, the cause of the problem was verified and identified through mold flow analysis. Wall thickness analysis revealed uneven distribution of the product wall thickness at the location of the defect. Further examination of the product filling results revealed that the material flow in this area was disordered, and the surface temperature of the material melt decreased too quickly and too low when passing through the rib, forming cold material, which prevented it from fusing well with the melt in other directions, So it produces cold material marks with others.
Optimization plan:
Thicken the flow channel at the cold material location to ensure the temperature at which the melt converges in all directions. The flow marks on the surface of the connecting reinforcement can also accelerate the filling of the main surface area, thereby shifting the fusion position to the connecting reinforcement position .
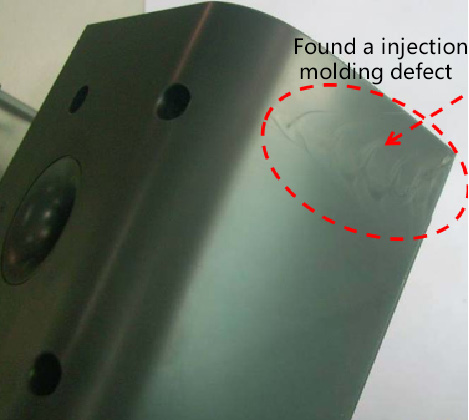

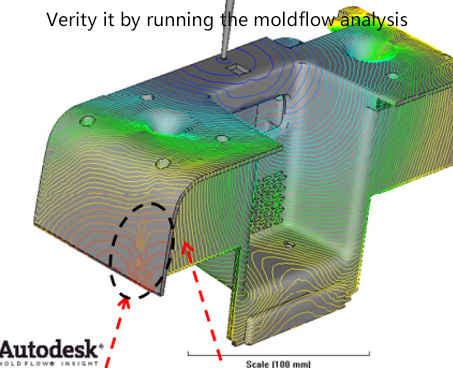

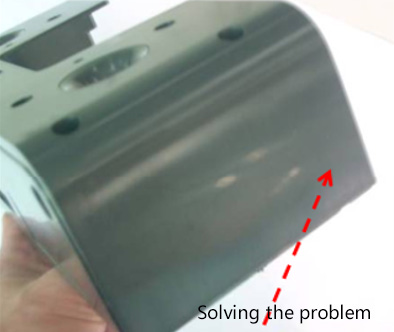

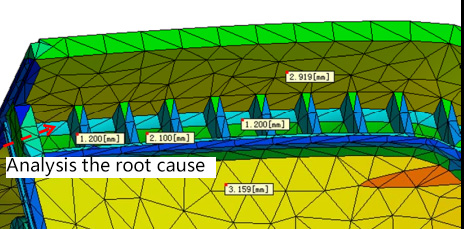