What are the reasons for the poor precision of injection molded parts?
Common injection defects are unqualified in size. The main reasons for analysis are: mold design and manufacturing accuracy problems, molding process conditions cause obvious changes in product shrinkage, uneven product shrinkage caused by molding materials, continuous changes caused by environmental conditions after molding, etc. .
1.The
machining accuracy of each part of the mold directly affects the dimensional
accuracy of the product. The core and cavity assembly, the position of the
parting surface, the design of the side slider, etc. will cause dimensional
errors. The long-term use of the mold will be affected by the cavity pressure.
, Clamping force and other factors cause mold deformation or relaxation, the
strength of the mold material and heat treatment must be considered when
designing the mold.
2.The
shrinkage of injection molded parts is caused by the change of melt density
when the plastic is cooled from the molding temperature to the ambient
temperature. It is not only related to the change of molding temperature, but
also related to the constraints of the product. When designing the mold, the
injection mold, the designer, The influence of process conditions and material
shrinkage must be considered comprehensively, as well as the cooling water
circuit design, the geometry of runners and gates, etc. For multi-cavity molds,
the cavity layout should also be optimized to ensure the thermal balance of the
mold system temperature, and the cooling water circuit design of the core and
cavity should be optimized to ensure uniform mold temperature.
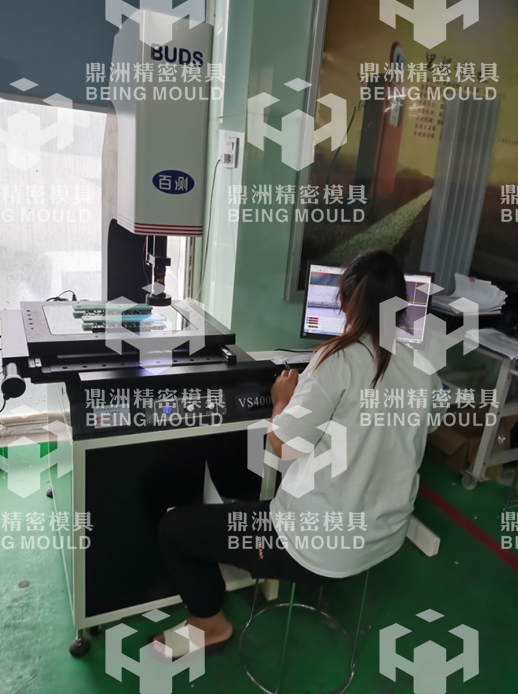
Share to: